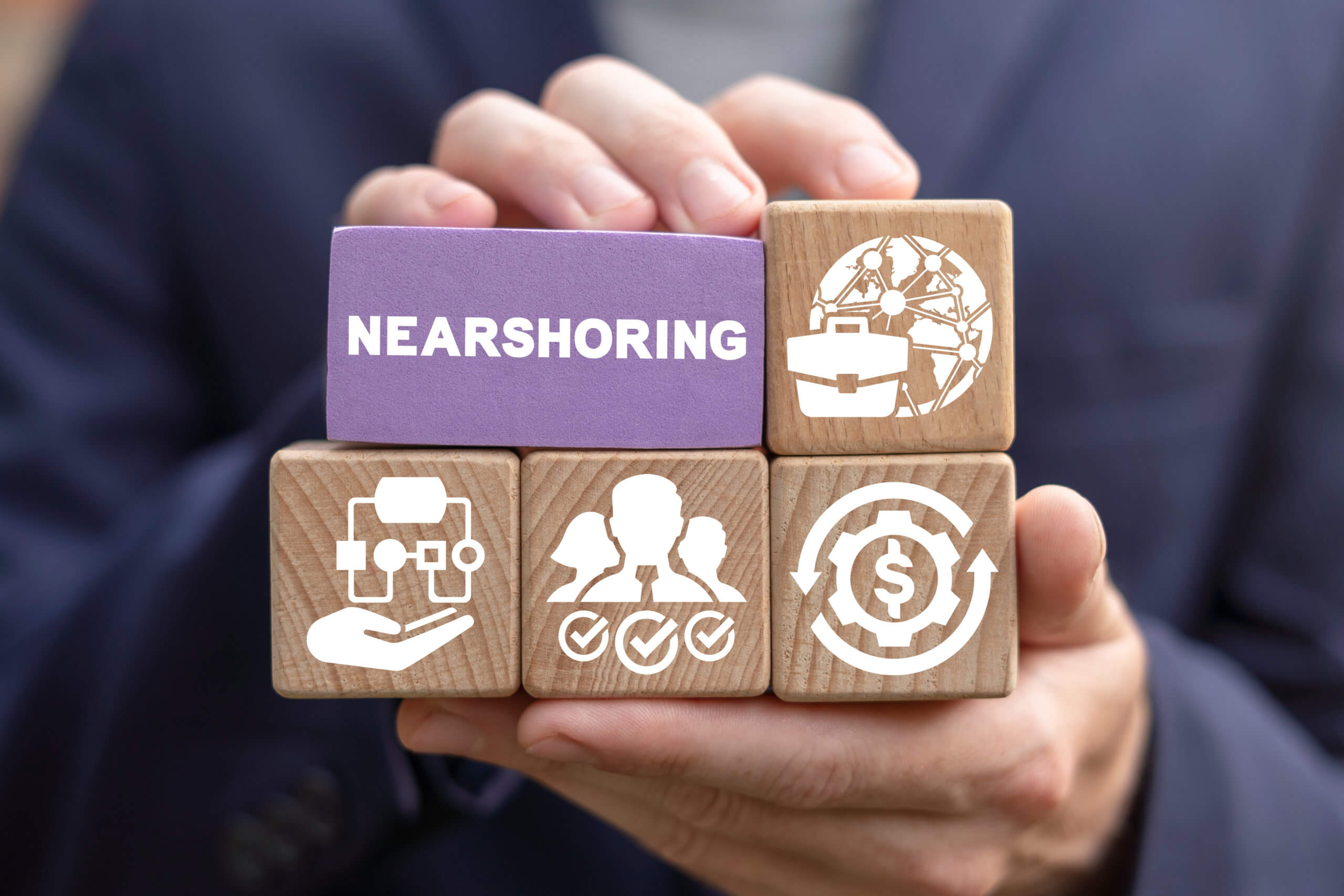
U.S. companies are reshoring at a historic rate. According to a Reshoring Initiative Report, about 1,800 firms plan to bring supply chains and workforces back home, opening about 350,000 additional jobs — the highest recorded number of reshored jobs since 2010.
Companies reshore due to:
- disrupted global supply chains sparked by the pandemic and exacerbated by weather disturbances
- geopolitical tensions
- fluctuating international trade.
These issues triggered a domino effect that led companies to deal with shipment delays, cross-border transit problems, empty stock shelves, steep tariff hikes, a higher total cost, and other significant challenges. Companies in North America see reshoring as a way to mitigate risks and take control of their end-to-end supply chains.
Amid Labor Shortages and Skyrocketing Costs, Is Reshoring Practical?
The straightforward answer is no.
In an ideal world, moving operations back to one’s home country can help many companies maintain as much control as possible. However, the economic and labor market climates have been less than ideal in recent years.
American markets face one major problem: the current labor crisis.
According to the Bureau of Labor and Statistics’ labor turnover report, on the last days of July 2022:
- The unfilled job openings in the U.S. were still above pre-pandemic levels at 11.2 million.
- The number of hires remains stagnant at 6.4 million.
- Separations were at 5.9 million, of which 4.2 million were voluntary quits.
From averaging 6.21% since 1960, salary growth in the U.S. reached an all-time high of 15.31% in April 2021. Still, the increase is insufficient to keep up with the country’s inflation rate, which saw a four-decade high of 9.21% in June 2022.
What about tax perks?
To motivate businesses to consider reshoring production, the government introduced policies incentivizing companies that keep manufacturing and distribution within America’s borders.
However, these perks may not cover the costs of running all operations domestically, especially for enterprises that need more resources to compete with large corporations.
Read More: Why Nearshoring to Colombia Is an Excellent Strategic Option for US Businesses
Nearshoring vs. Reshoring: Is there a more “inflation-friendly” response to the supply chain disruption?
Instead of bringing manufacturing operations back home or taking their business overseas to places like China, many companies opt for nearshoring as an alternative.
What is nearshore outsourcing?
Nearshoring means outsourcing company operations to nearby countries, whether in part or whole. Usually, nearshoring destinations are within the same region as the client’s country of origin. Colombia, Costa Rica, Mexico, and other countries in Latin America are among today’s most popular nearshoring options.
Although nearshoring and reshoring are both viable options for companies looking to bring suppliers closer to home and address supply chain challenges, there are various reasons why outsourcing to a foreign country located nearby is still the better option.
Why Nearshoring Is the More Practical Response to Supply Chain Disruptions
1. Nearshoring is more economical.
Bringing production back home can cost companies at least three to five times more for labor alone. Across industries, U.S. companies struggle to hire and retain workers, resulting in rising labor costs that contribute to the rising prices of nearly everything.
With nearshore outsourcing, a manufacturing company can gain significant savings compared to establishing operations in-house or onshore. For example, let’s compare the salary of one of the most in-demand jobs in the U.S. today.
As of May 2021, the median annual salary for software developers, analysts, and testers in the U.S. was $109,020. Meanwhile, in some Latin American countries, the median annual wage for software engineers was between $4,000 and $50,000 (as of June 2021).
Since the outsourcing country is nearer, nearshoring gives businesses virtually all the benefits of reshoring — minus the higher cost. These benefits include:
- Avoiding shipping delays of raw materials, components, and finished goods
- Better control of processes
- More convenient time zones
- Reduction of external risks
- Lower labor costs, travel costs, and logistics costs
- Faster turnaround times
2. Nearshoring expands your talent sources outside your borders.
Industry analysts foresee labor shortages causing seismic economic disruptions beyond 2022. While automation may work for essential manufacturing tasks, it can only cover some of the skills required to run an efficient onshore or in-house operation.
Additionally, the reshoring process itself requires significant human resources. Manufacturers have to quickly fill numerous positions essential to completing a seamless relocation, from building factories to finding suppliers and ensuring logistics management continuity.
Meanwhile, moving production nearshore allows you to diversify talent sources beyond your borders while tapping into talent-rich markets and niche expertise.
For example, Colombia is among the most sought-out destinations for high-end developers. Home to excellent tech institutions, the country produces about 13,000 software developers yearly.
Read More: 4 Signs Proving That ‘The Great Resignation’ Is Far From Over
Aside from tech professionals, other functions ideal for outsourcing to Colombia include:
-
Multilingual Customer Support
More than 99% of Colombians speak Spanish, one of the most widely spoken languages in the world. Many are bilingual since English is part of Colombia’s primary education curriculum.
-
Cybersecurity and Information Technology
Colombia’s internet and network infrastructures are among the most impressive worldwide. This clout, along with human resource availability, is one of the reasons why the county topped the 2021 BPO Offshore Confidence Index.
-
Logistics and Back Office Support
During the initial phases of outsourcing, South America was among the pioneer destinations for manufacturing-related back-office functions. Workers in the country have comprehensive knowledge of retail, automotive, manufacturing, and other industry-specific jobs.
3. Nearshore outsourcing enhances operational resilience.
While moving production onshore may bring local products to store shelves faster, it cannot (on its own) help manufacturing companies keep pace with modern consumers’ changing behavior. It also doesn’t guarantee supply chain resiliency.
In a 2020 Forbes study, 86% of consumers were willing to pay more for a great customer experience. Today, U.S. consumers prioritize affordability, switching to brands offering lower prices while expecting an excellent customer experience.
You’ll end up overproducing and draining your cash flow if your production process is not flexible enough to respond to market demands.
Through nearshoring, businesses can swiftly adjust to fluctuating consumer demands and enjoy greater access to scalable staffing and other resources. It is also more cost-efficient, helping you enhance cash flow resilience to weather unprecedented supply chain disruptions.
Read More: How Offshoring and Onshoring Services Can Be a Viable Staffing Solution for Companies of All Sizes
If you’re stuck choosing between offshoring, reshoring, or nearshoring, why not have the best of all worlds?
The supply chain ecosystem has become more intricately interconnected as the world becomes increasingly globalized. Diversifying business models is critical to remain agile and competitive.
Why not combine offshore, onshore, and nearshore outsourcing to cover all bases? In most cases, you can keep about 25% of the core workforce onshore, offshore 50% of the remaining crew, and nearshore all the rest.
If your industry requires you to keep most operations onshore, consider delegating about 10-15% of support functions offshore and about 5% nearshore as a buffer.
If the distance between the manufacturing plant and your customers is crucial to your business, consider nearshoring your core functions and offshore all support tasks with about 5% onshore as a buffer.
These are just some of the possible scenarios. It’s best to consult the experts to know the ideal outsourcing strategy and workforce composition for your specific business.
Develop Your Ideal Continuity Plan
Improve your operational flexibility and future-proof processes in case another global supply chain crisis hits—partner with a BPO provider capable of meeting your onshoring, offshoring, and nearshoring needs.
A presence in key outsourcing countries can enable you to tap into a rich pool of global talents while overcoming various international and domestic challenges.