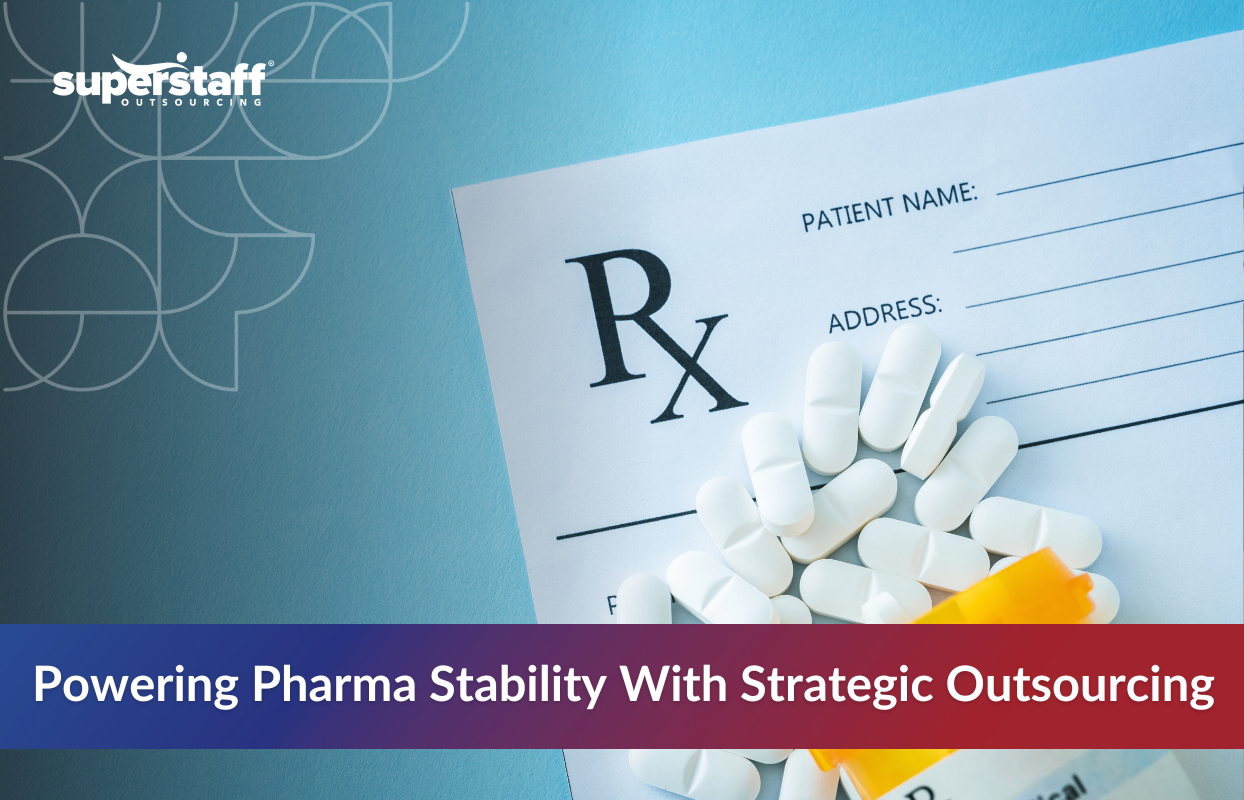
When the supply chain in the pharmaceutical industry stalls, patients feel the pain — literally.
In 2025, the supply chain in pharmaceutical industry faces one of its most serious challenges. With the U.S. trade war escalating, geopolitical tensions have disrupted the global flow of raw materials and finished medications. Active pharmaceutical ingredients (APIs) sourced from overseas are caught in a web of tariffs, export restrictions, and border delays. Meanwhile, the slowdown in manufacturing and delivery of essential prescription drugs creates ripple effects, from rising costs to critical shortages that directly impact patient care.
This blog explores how outsourcing can serve as a strategic solution to ease the pressure. By shifting non-core functions, compliance processes, and even customer support to trusted outsourcing partners, pharmaceutical companies can regain control, streamline operations, and better support healthcare providers and patients.
As the supply chain in the pharmaceutical industry becomes increasingly volatile, outsourcing isn’t just a cost-saving tactic — it’s a lifeline for operational resilience, regulatory compliance, and continuous patient access to life-saving medications.
The 2025 Trade War Has Amplified Supply Chain Vulnerabilities in the Pharma Sector
The intensifying U.S. trade war has thrown global pharmaceutical supply chains into disarray, revealing structural weaknesses many companies can no longer overlook. From sourcing disruptions to skyrocketing costs, every link in the pharma supply chain is under pressure, and patients are feeling the effects.
Scarcity of Active Pharmaceutical Ingredients (APIs)
Many U.S. pharmaceutical companies depend on international partners, particularly in Asia, for the production of APIs — the essential building blocks of most medications. The benefits of outsourcing pharmaceutical production overseas have long included cost efficiency, access to specialized manufacturing capabilities, and faster scalability.
However, these global sources are becoming increasingly unreliable with trade restrictions tightening and diplomatic tensions escalating. Export bans, tariffs, and raw material shortages in supplier countries lead to widespread API scarcities. As a result, drug manufacturers are now grappling with production delays, limited batch runs, and stalled timelines for new and existing treatments, putting the long-standing advantages of global production to the test.
Regulatory and Customs Bottlenecks
Even when supplies are available, getting them into the United States has become a logistical minefield. Customs procedures have become more complex, with new documentation requirements and shifting compliance standards introduced in response to the trade conflict.
These regulatory barriers are causing significant hold-ups at borders and ports. Shipments that once moved seamlessly through global transit networks are now facing extended clearance times, creating inventory imbalances and gaps in regional drug availability. The inconsistency disrupts supply chains and hinders demand planning and pharmacy-level distribution.
Soaring Production and Freight Costs
Rerouting shipments, sourcing from new suppliers, and responding to tighter regulations all come at a price. Pharmaceutical companies face steep increases in production and freight costs as they scramble to adapt to ongoing disruptions.
For temperature-sensitive drugs, the challenges are even more significant. Cold chain pharmaceutical logistics, which ensure medications are stored and transported within strict temperature ranges, add another layer of complexity and expense. Alternative shipping routes often require longer transit times, specialized handling, and higher insurance premiums, which strain budgets and increase operational risk.
As these costs climb, drug prices rise, and access becomes more limited, particularly for patients who rely on critical, high-cost medications that cannot withstand even minor supply delays or temperature fluctuations.
Mounting Risks for Public Health
The cumulative effect of these disruptions is more than operational — it’s a growing threat to public health. Drug shortages are leading to postponed treatments, emergency substitutions, and delays in chronic care management. For healthcare providers, the lack of availability adds stress to already stretched resources and forces difficult decisions that can impact patient outcomes.
Why Pharma Companies Must Act Now
The pharmaceutical sector is at a turning point. Traditional sourcing and distribution strategies no longer provide the reliability companies need in a politically volatile world. To protect their operations — and the patients who rely on them — pharma leaders must rethink how they manage their supply chains.
The path forward requires agility, speed, and access to specialized expertise. Outsourcing has emerged as a powerful strategy to fill the operational gaps exposed by the trade war — and to build the resilience needed for an uncertain future.
Outsourcing Pharmaceutical Logistics Helps Companies Navigate Disrupted Supply Routes
When conventional shipping routes become unreliable, outsourcing healthcare logistics becomes more than a convenience — it becomes a necessity.
Specialized third-party logistics partners can offer the agility and oversight pharma firms need during a crisis. With deep experience in regulated environments, these partners manage mission-critical tasks such as:
- Track & trace services that monitor every movement of high-value shipments.
- Dispatch coordination using alternative lanes, minimizing delays and bottlenecks.
- Proof of delivery (POD) verification, ensuring full compliance and secure chain-of-custody.
But even with meds en route, that’s only part of the solution. The next priority is keeping patients and providers in the loop.
Outsourced Customer Support Teams Can Help Manage Patient and Provider Communication During Shortages
Shortages create uncertainty. Patients want answers. Providers need clarity. And pharmaceutical companies must be ready to deliver both, especially as disruptions in the supply chain in the pharmaceutical industry continue to escalate.
Outsourced customer support plays a vital role in bridging the communication gap. These dedicated teams ensure that no call for help goes unanswered, particularly when treatment decisions rely on up-to-date information. Outsourcing partners can:
- Provide 24/7 hotline support for pharmacies, clinics, and patients seeking updates.
- Use customized scripts to explain delays and suggest safe alternatives.
- Offer multilingual assistance to reach communities across diverse and impacted regions.
As the supply chain in the pharmaceutical industry becomes more complex, clear and compassionate communication helps ease frustration, maintain trust, and protect brand reputation. Still, even the best communication strategies must be backed by accurate documentation, which is where outsourcing compliance support becomes essential.
Data Entry and Compliance Outsourcing Ensures Reporting Accuracy and Audit Readiness
In pharma, paperwork isn’t just paperwork — it’s a legal and ethical obligation.
During disruptions, outsourcing compliance support ensures that companies meet evolving requirements while maintaining operational focus. Trusted back-office teams assist with:
- Real-time updates to inventory and forecast systems, keeping distributors informed.
- Documenting drug substitutions and justifications, critical for regulatory audits.
- Staying compliant with FDA, EMA, and other global standards, even as rules shift.
With processes documented and systems updated, pharma companies can focus on what they do best — science and safety.
Outsourcing Builds Long-Term Resilience for Pharmaceutical Companies Facing Global Disruption
Outsourcing isn’t just a stopgap solution — it’s a long-term growth strategy designed for today’s volatile environment.
As disruptions continue to expose weaknesses in the supply chain in the pharmaceutical industry, outsourcing allows companies to stay agile and focused. Pharmaceutical leaders can redirect internal resources toward R&D, innovation, and regulatory strategy by offloading high-volume, process-driven tasks.
Key benefits include:
- Scalable support teams that can ramp up quickly during spikes in demand or unexpected disruptions.
- Access to global talent pools with deep expertise in healthcare operations and regulatory compliance.
- Faster adaptation to shifting compliance requirements and new market conditions.
SuperStaff understands the evolving complexities of the supply chain in pharmaceutical industry operations, and we’ve built solutions specifically designed to meet them head-on.
SuperStaff Provides End-to-End Outsourcing Solutions for Pharmaceutical Supply Chain Resilience
SuperStaff works with pharmaceutical and healthcare companies to design outsourcing solutions that keep operations compliant, consistent, and connected — even in turbulent times.
With delivery hubs in the Philippines and Colombia, we support clients across logistics, CX, and back-office functions. Our value lies in:
- Trained teams familiar with regulated environments and HIPAA-compliant workflows.
- Flexible solutions to meet immediate disruptions and long-term growth.
- Full transparency, including detailed reporting, dedicated account management, and built-in compliance support.
As the trade war continues to shape pharmaceutical operations, action is the only antidote to inaction.
Outsourcing Isn’t Just a Fix — It’s the Lifeline for the Supply Chain in the Pharmaceutical Industry
The 2025 trade war is straining the pharmaceutical supply chain, but outsourcing offers a practical path to stability and service continuity.
From logistics and communication to compliance and flexibility, outsourcing enables pharma companies to keep patients supported, products moving, and operations aligned with strict regulatory standards, even during unpredictable conditions.
Ready to protect your pharmaceutical operations from trade war fallout? Partner with SuperStaff for reliable, scalable support where and when it matters most.